以前DMM.makeに発注して到着したドローンのフレームを見て,たくさん改善点があるなと思いました.
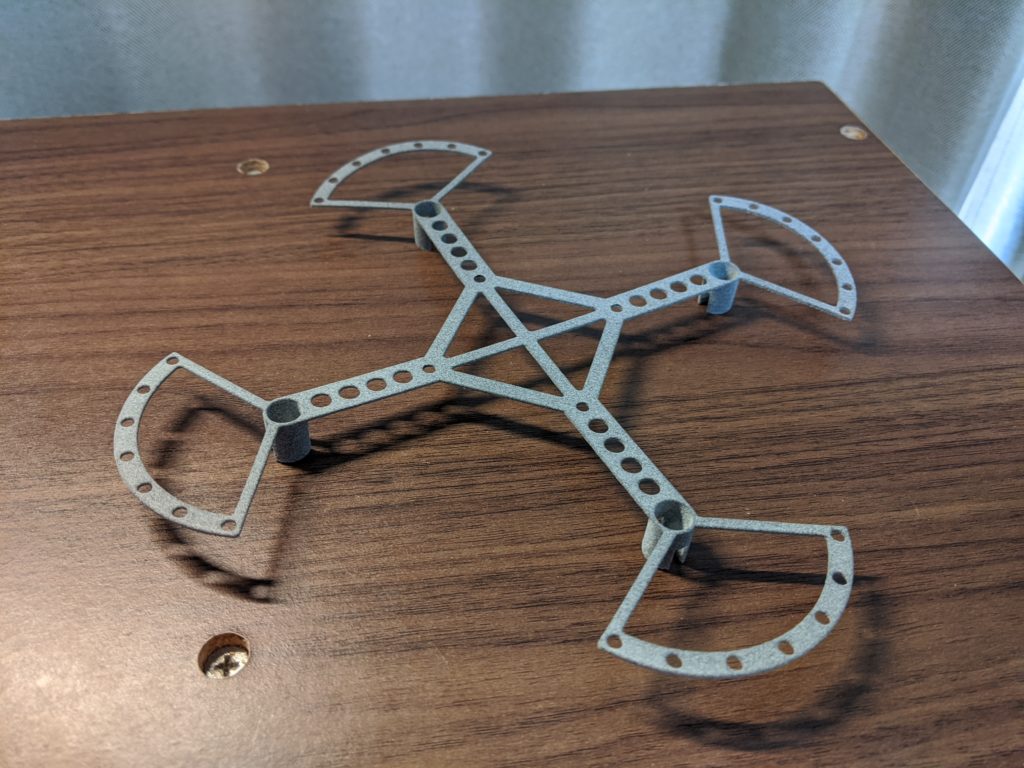
改善点を並べてみると以下のようになります.
- モータとモーターブラケットの間隔が広い(モータがぶかぶかになっている)
- 全体としてもう少し小さくできそうなので,小さくする
- 45 x 45 mmの基板に回路を乗せるため,それ用に寸法を合わせる
- 脚をつけるためのねじ穴を用意する
- filletはいらない(あまりfilletがあることによるメリットを感じなかった)
- モータを固定する用に,上からモータブラケットをかぶせる
- プロペラガードの重みでホバリングできない可能性があるので,プロペラガードは着脱可能とする(プロペラガード + 固定用のネジで5 gほどあった.)
- 可能な限りFreeCADのSketchの数を減らし,設計を簡便化する
- 機体フレームの剛性が弱くてふにゃふにゃ
加えて,今回はアセンブリによって発注予定の部品の寸法が誤っていないかも確認してみました.いいかんじのFreeCADのAssembly3の解説動画や解説サイトを見つけられなかったので,直感で操作しました.自分の使いたい機能は使えたと思います.備忘録として手順をまとめておきます.
機体フレームの剛性解析に関しては以下の記事でまとめてみたので,よければご覧ください.
完成したパーツ
先に,今回の設計見直しでできあがった個々のパーツのデザインをアップします.1つ目と4つ目のstlファイルをDMM.makeさんに3Dプリント依頼します.

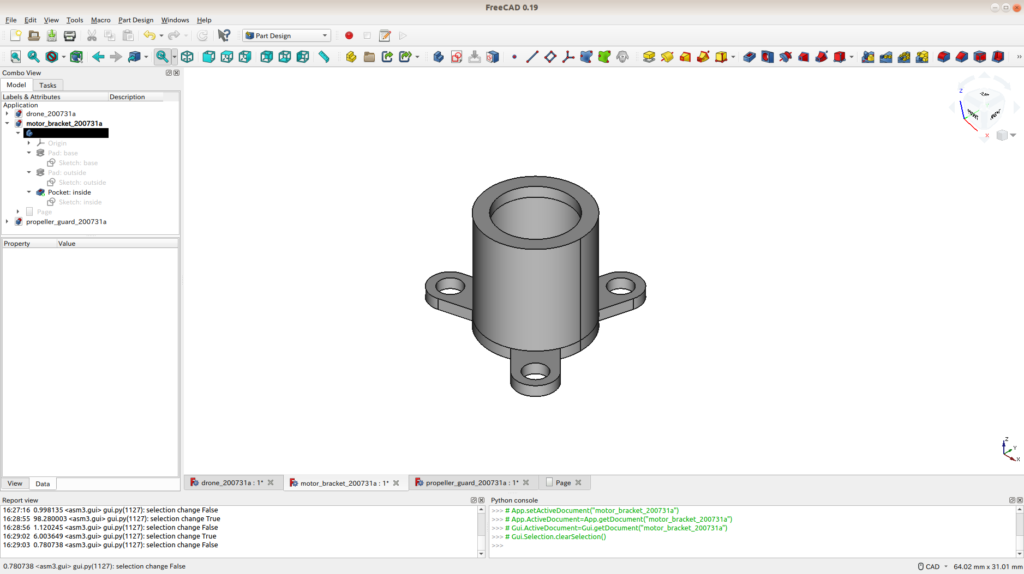
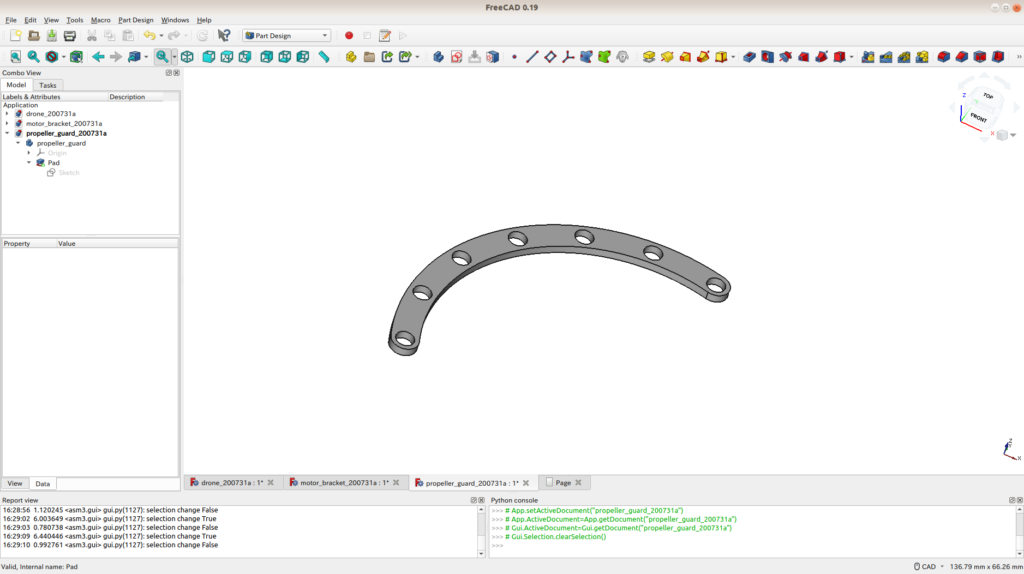
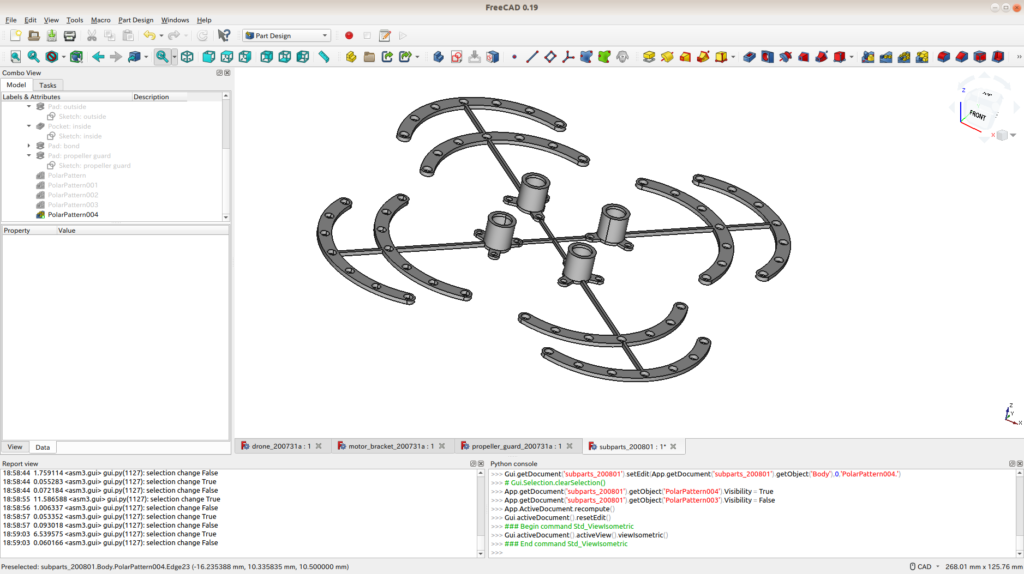
細かい変更
ベースの設計図はこんな感じになりましたが,正直ごっちゃりしすぎてて何がなんだかわからないので個別に要点だけ書いていきます.
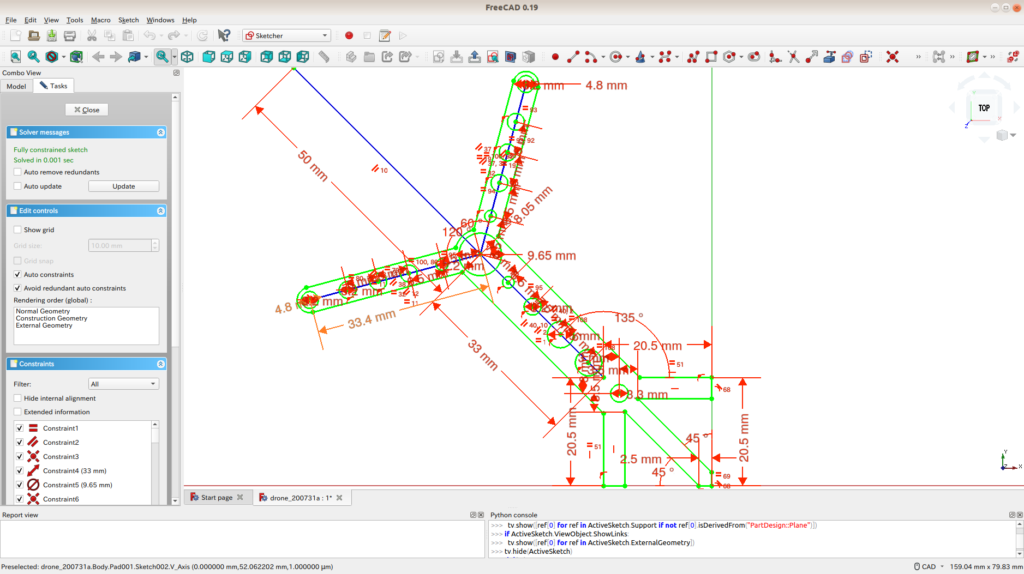
モータとモーターブラケットの間隔
モータの直径は8 mmで,前回発注したボディでは,モータを格納する部分を8.4 mmにしたところ,思いの外ぶかぶかになってしまいました.
そこで今回は,モータブラケットの内径は8.05 mmとしました.もし,3Dプリンタの出力誤差でモータが入らなかったらヤスリで削ります.また,モータブラケット外形は9.65 mmとします.前回発注したときに壁の最小厚さは0.8 mmとわかったので,外形の半径を+0.8 mm(直径を+1.6 mm)します.
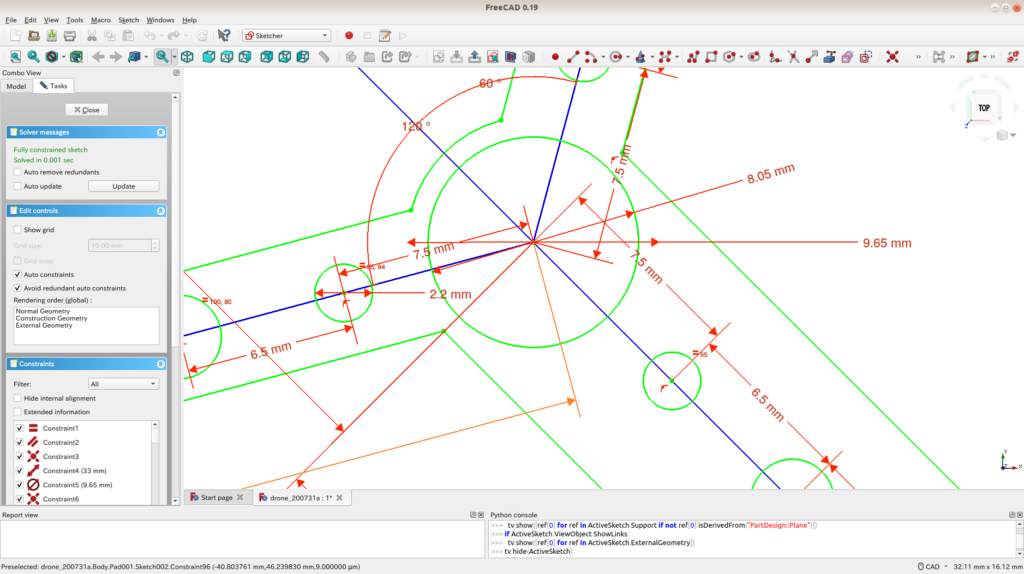
45 x 45の基板をのせる
今回ユニバーサル基板として,以下のものを使用する予定なので,機体中心から,穴までの距離を17.5 mmにする必要があります.
ちょっとわかりにくいですが,20.5 – 3 = 17.5 mmとなっています.
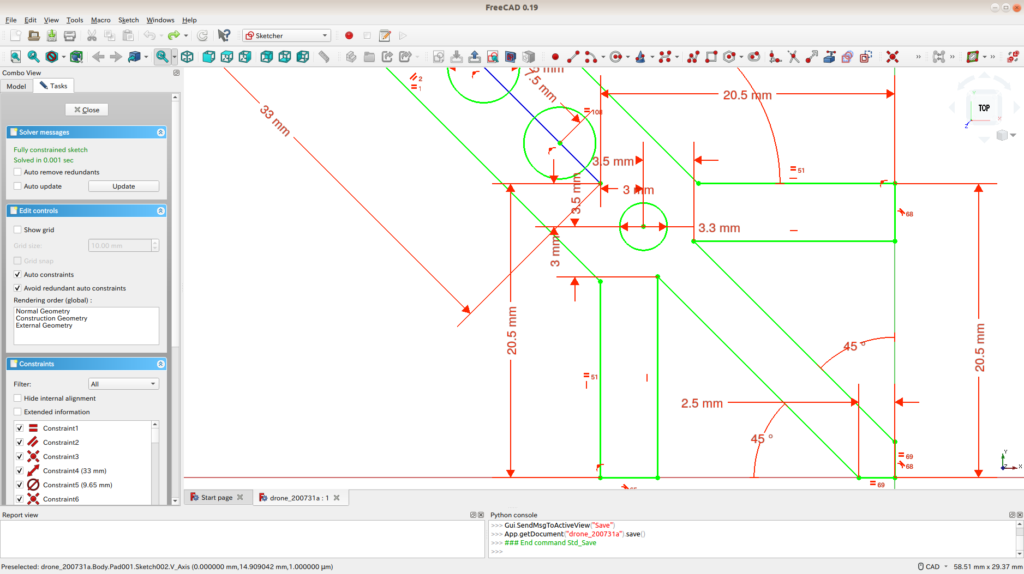
この基板を使うことにより,もとのサイズから6 mmほど小さくなりました.
脚をつけるための穴に関しては,ところどころに3.2 mmのネジ穴を機体にあけています.
モータ固定部
モーターを固定部は,以下の条件を満たす必要があります.
- モータは高さ20 mmなので,モータ固定部は内枠20.5 mm,外枠22.5 mmとする.
- モータを上から固定するパーツを作る.
- 直径5 mmのプロペラの軸受部分がモータ固定部と干渉しないようにする.
これらの条件をすべて満たすモータ固定部を絵にすると,以下のようになります.手書きなのでわかりにくいのはご容赦ください^^;;
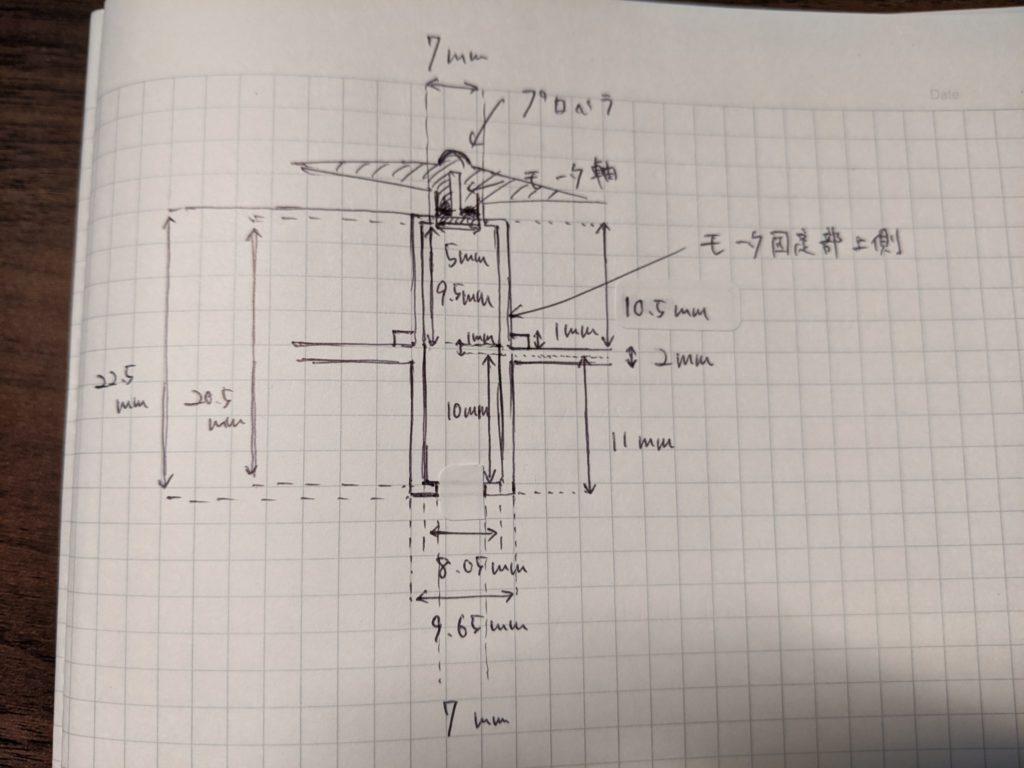
実際にこの仕様通りになっているかを図面を引いて確認してみると,大丈夫そうでした!
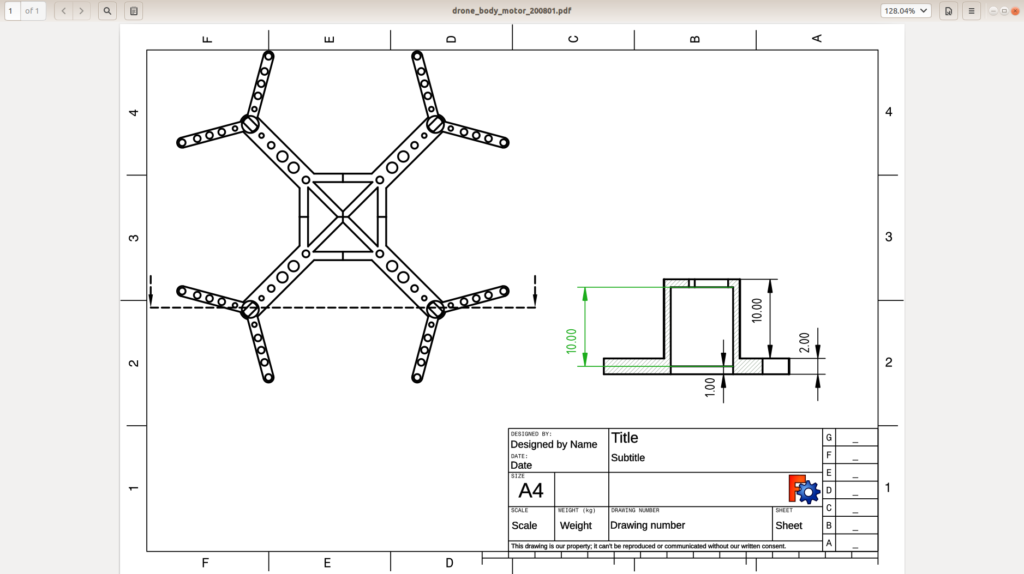
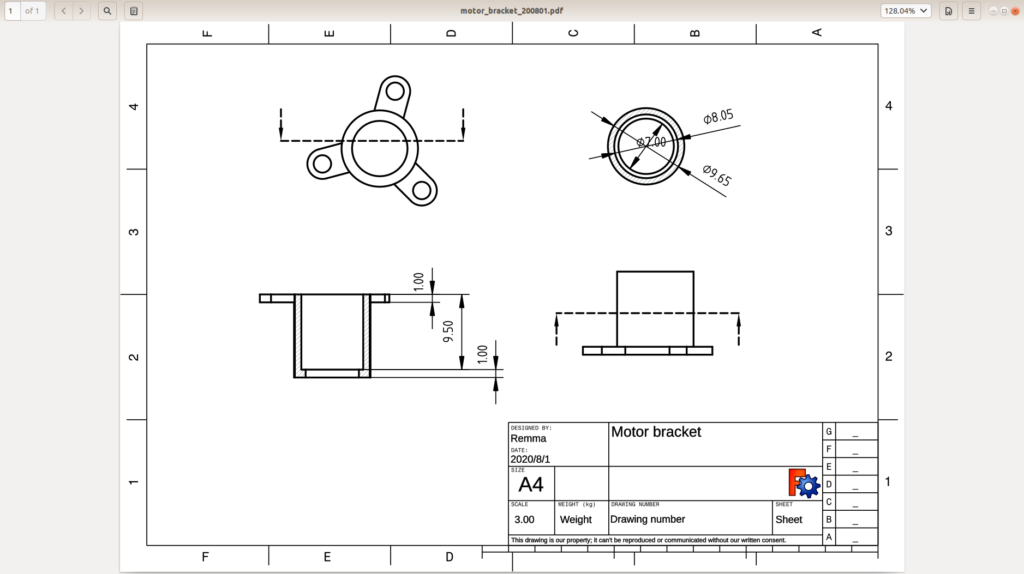
図面の引き方は以下のサイトがわかりやすいです.
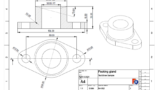
着脱可能なプロペラガード
前回はドローンの機体とプロペラガードを一体化させていましたが,今回はプロペラガードを別で作成し,これをネジ止めする設計としました.
アームの端にプロペラガードを取り付けます.
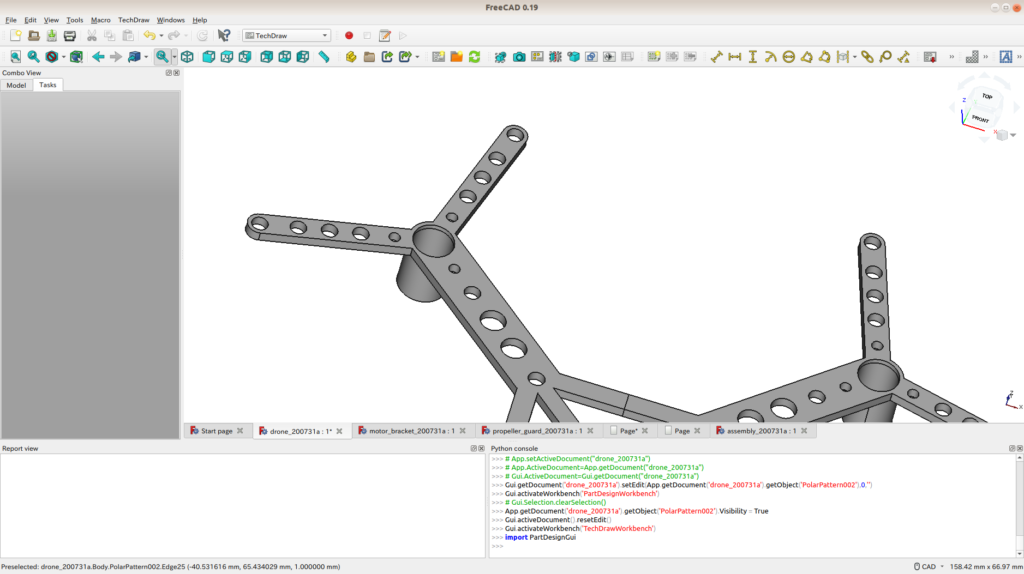
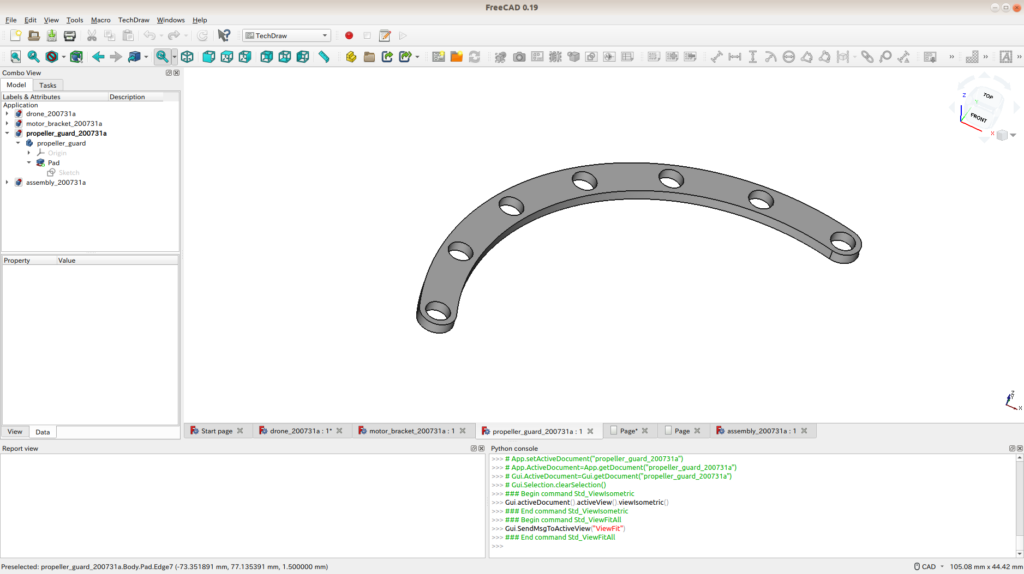
Sketchの数を減らして設計を簡便化
下の図を見れば一目瞭然かと思いますが,今回は前回の設計と比べて,部品点数が少なくっています.部品点数を少なくすることで,設計の見直しを容易にしました.たとえば,前回の設計では機体のベース・ベースの肉抜き・アーム・プロペラガードをそれぞれ別のSketchで描いていましたが,今回はこれらを統合して1つのSketchにまとめています.
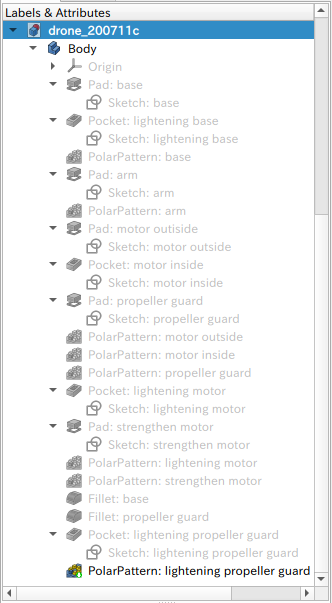
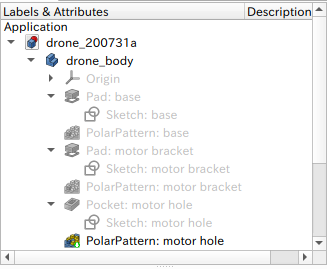
アセンブリ
Assembly3でのアセンブリの方法について以下でまとめます.
①「Assembly3」を選択し,「Create assembly」を実行します.
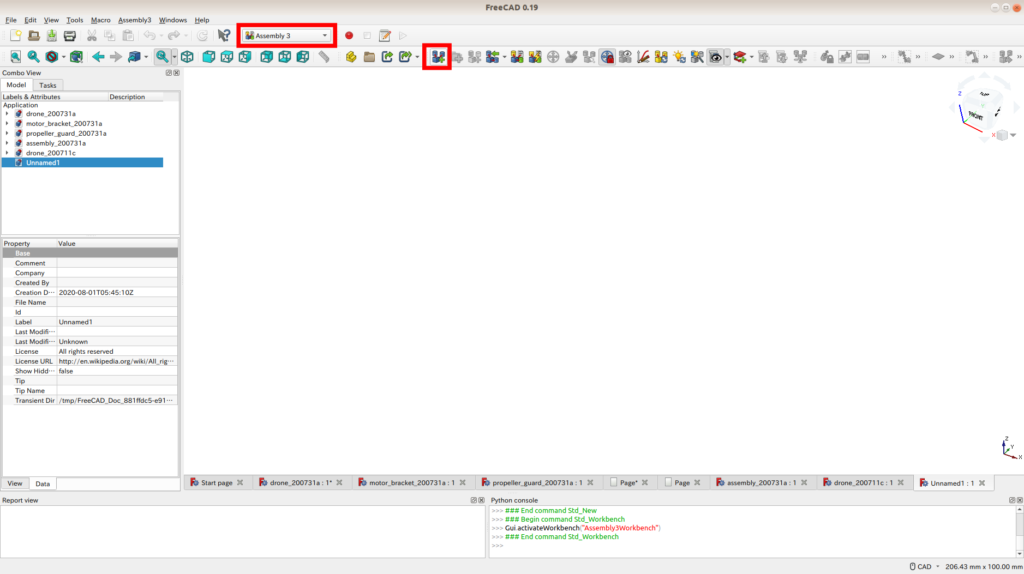
②アセンブリしたいパーツを「Assembly」の「Parts」にコピーします.今回は下図の青色の部分をくっつけたい場合を考えます.
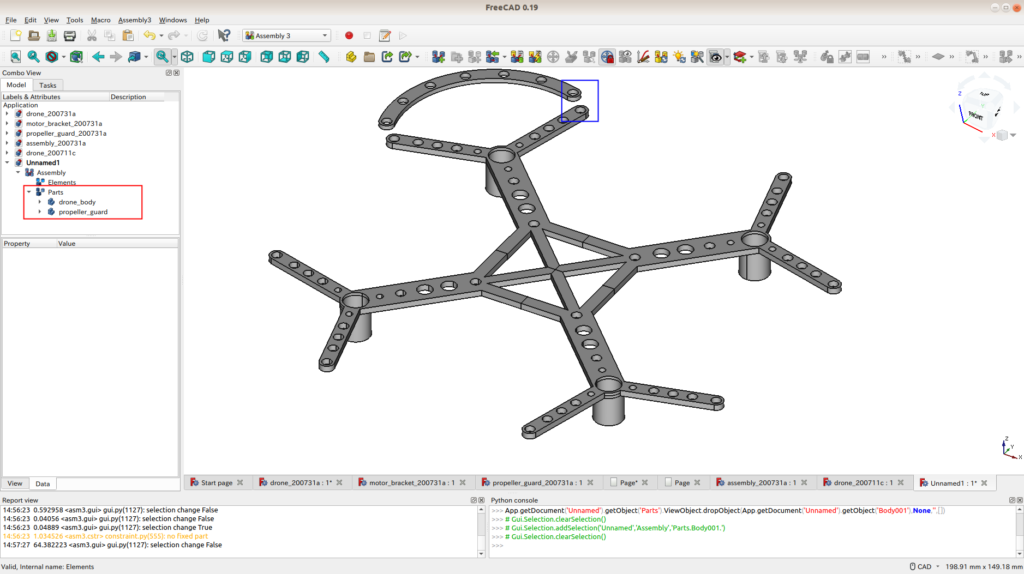
③Ctrlボタンを押しながら2つのパーツのくっつけたい部分を選択し,黄緑になっていることを確認します.
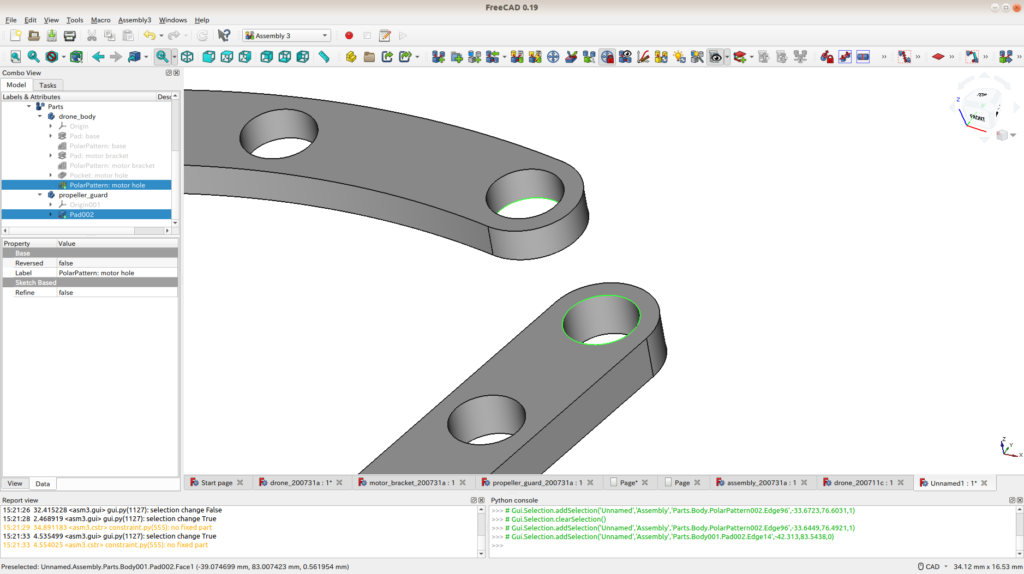
④「Add Attachment contstraint」を選択します.
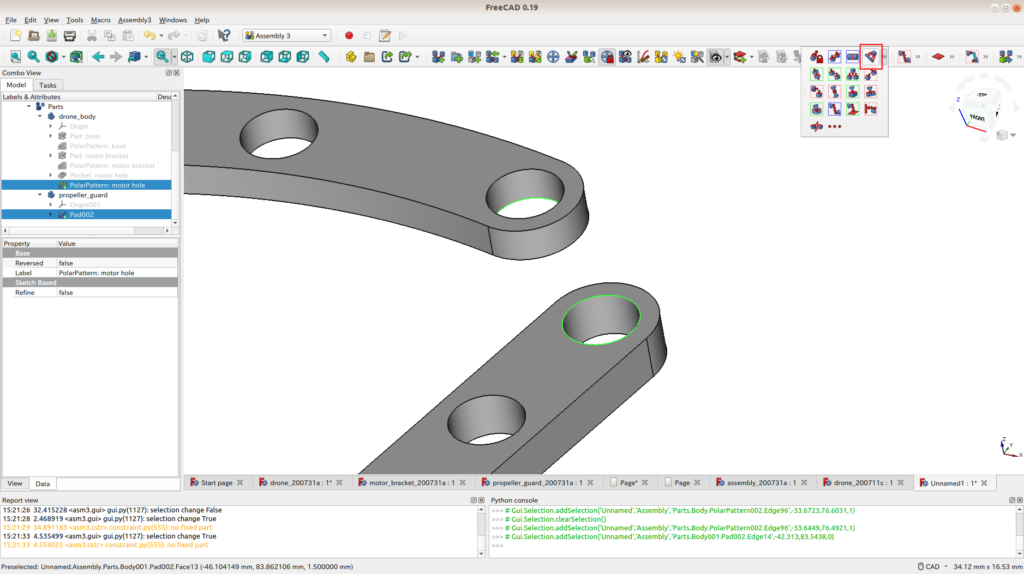
⑤最後に「Solve constraints」を実行すると,2つのパーツがくっつきます.
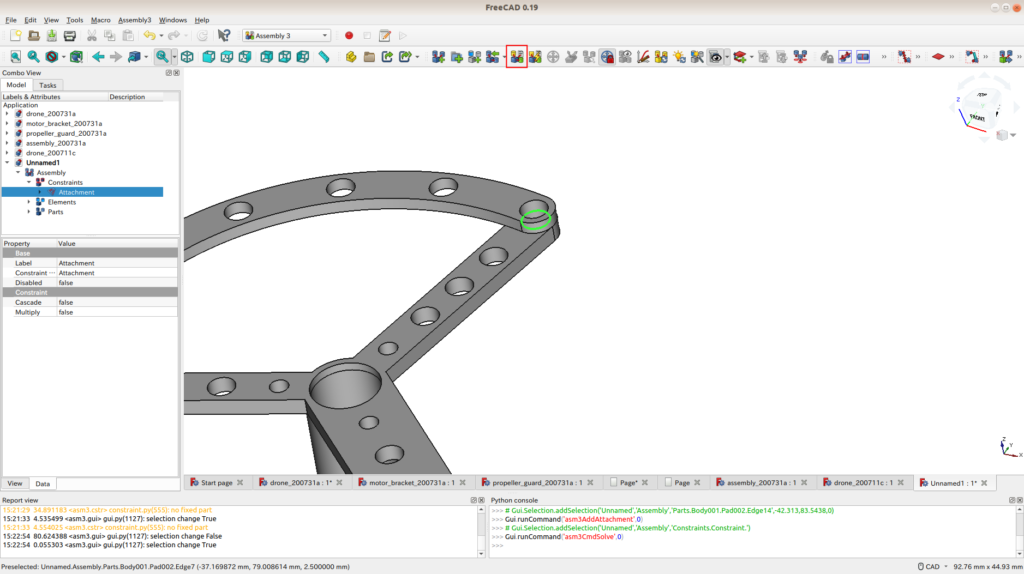
ポイントは,Add constraintsだけでは制約が実行されないので,Solve constraintsボタンを押さなければならないということです.
アセンブリの完成図が以下です.寸法的なズレがないことがわかりました.
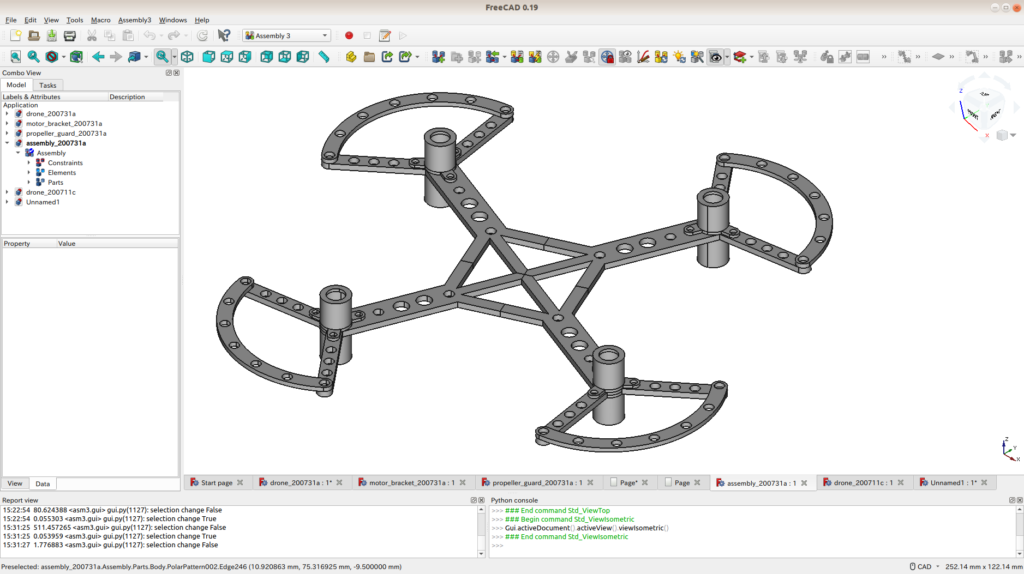
推定重量
前回の発注でpa12gbという素材で機体を発注しました.この機体が5 gで,体積は5.15 cm^3だったのでpa12gbの密度は約1 g/cm^3と推定されます.今回もこの素材で発注予定なので,pa12gbで3Dプリントすることを前提に推定重量を計算します.機体フレームの厚さを1 mmから2 mmにしたので,予想としては,重さが2倍程度になりそうです.
今回のパーツの体積は以下のようになりました.
ボディ | 6.72 g/cm^3 |
モーターブラケット | 0.28 g/cm^3 |
プロペラガード | 0.45 g/cm^3 |
組み立てるときは,ボディ x 1 + モーターブラケット x 4 + プロペラガード x 8で機体を作成するので,これを計算すると,
6.72 + 0.28 x 4 + 0.45 x 8 = 11.44 cm^3
になります.重さは約11.44 gになりそうです.予想よりも少し重くなりました.
まとめ
- 1回目の設計から改変すべきところを改変しました.
- アセンブリをして寸法に誤差がないか確かめました.
- 推定質量を計算しました.
コメント